Debar embeds a culture of continuous improvement
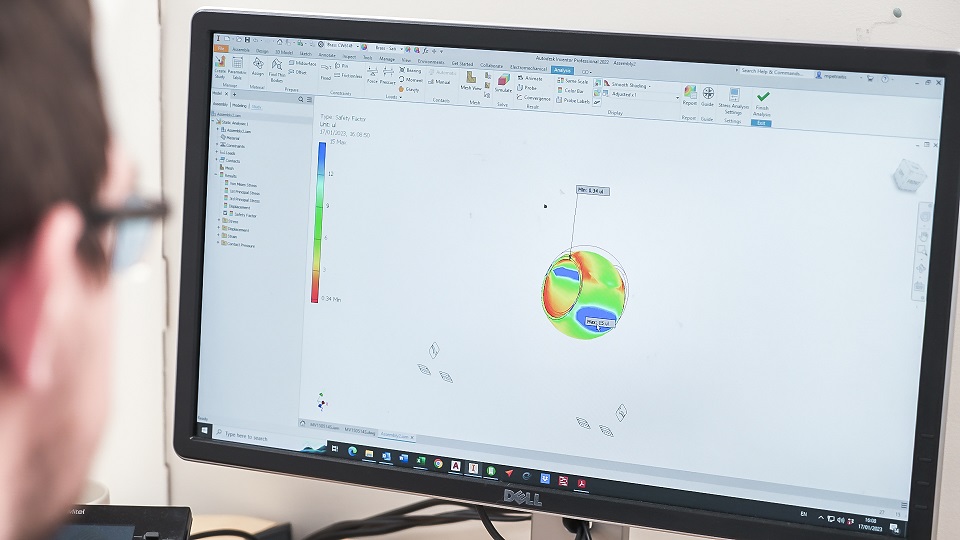
Debar is the UK’s leading independent designer of bi-fold systems and a solid supplier of quality hardware and components. The Bradford-based company supplies to more than 200 companies across 12 countries, gaining a well-deserved reputation for reliability, robust products and outstanding customer care.
The question is how have they done this in just 15 years of operating within the bi-fold door market? Well, a commitment to continuous improvement has been the key to Debar’s success.
Not content to be a ‘one-item’ company, over the years Debar has made sure it is ahead of the curve both in terms of keeping up with market trends and extending its product knowledge to system houses and fabricators looking to know more about the bi-fold industry.
For Debar, continuous improvement is not about growing a company at a rate of knots while seeking ever bigger profit margins. Instead, it’s centred around making gradual improvements over time and empowering employees to innovate and ‘own’ workplace change. Continuous improvement requires good communication across the company, plus close analysis of results to see if such changes are having an effect in the market.
Over the years Debar has developed a portfolio full of achievements and innovations which proves their continuous improvement policy is incredibly effective. One of these is how the organisation achieved the coveted ISO9001 certificate. This international standard proves Debar consistently provides products and services that meet both customer need and regulatory requirements. In other words, commitment to quality management in all areas of the business.
Communication is key
In terms of communication, Debar’s internal suggestion programme has led to the development of several in-house projects which have been introduced this year. This includes rearranging the layout in both CNC and assembly to improve efficiency and visibility of stock and improving work-life balance by introducing flexible working.
A true commitment from employees is also demonstrated in a cross-training matrix designed to improve job enrichment and create a more agile workforce better placed to be able to respond to fluctuations in demand.
Debar is currently putting together a ‘stage and gate’ process to encourage employees to present ideas for new products and improvements to existing products. Employee targets are constantly reviewed and a reward scheme has been introduced to recognise excellent performance.
Investing in innovation
Over the years, Debar has invested in the latest software and machinery to create innovative products and systems, while keeping up to-date with the latest industry trends to offer first-class advice and guidance.
For example, robotics have recently been introduced to cover monotonous tasks, allowing Debar to upskill its workforce, while waste has been reduced via new methods for product recovery and rework. This has had a significant impact on the drive toward improved sustainability. A ‘vision system’ has also been put in place to improve quality checks for incoming goods and in-process controls where tolerances on dimensions are critical.
The company’s commitment to innovation and improvement was also reinforced in 2017, when Debar moved to its present, 65,000 sq ft headquarters and manufacturing site in Bradford. This additional space was utilised for a new saw centre, CNC centre, finishing station, automated powder coating plant and assembly lines.
Even then, the company sought to improve on its offering by broadening its services to support system houses and fabricators looking to break into the bi-fold industry. Debar offers technical training and support to people wanting to learn more about bi-fold fabrication, hardware and components.
Ben Fawthrop, Operations Director at Debar, is keen to stress the company’s commitment to a 360-approach which aims to get the best out of its employees so that they pass on their passion and enthusiasm to Debar’s customers.
“We started out wanting to be more than just another manufacturing company and over the years we’ve shown that we can innovate in all sorts of ways. We’re constantly looking at how we can best serve our customers, so we are preparing a transformation from Quality Assurance to Total Quality Management to encourage a more engaged approach to meeting and exceeding customer expectations.
“We’ve also conducted a review of our transport and warehouse operations resulting in a redesign of the facilities and plans to introduce RFID and barcoding for stock movements and control.
“We’re an ambitious organisation, headed up by an experienced and dedicated management team and we have a workforce that is passionate about what we do and how we do it. Quality and service is at the heart of our offering, and it’s through a policy of continuous improvement that we’ve been able to make this real, time and time again.”
Debar is the leading independent British manufacturer of bi-fold hardware and bi-fold door systems supplying to fabricators and system houses around the world. For more information visit: https://www.debarhardware.com/
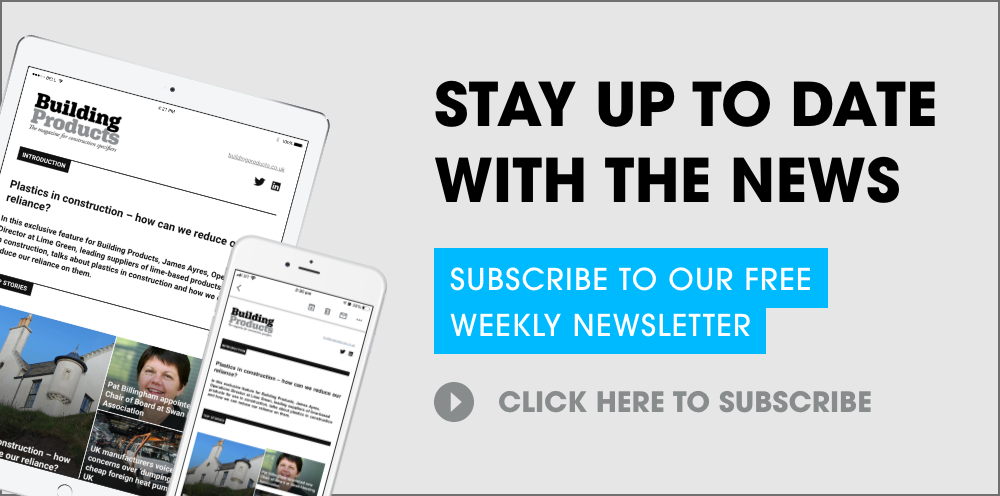