The advantages of flowing liquid gypsum screeds over sand and cement options

Ross Verity, managing director of ForceDry, explores the advantages of flowing liquid gypsum screeds over sand and cement options and explains why flowing gypsum screeds and the latest force drying technology are a winning combination.
Modern underfloor heating systems represent the height of luxury, comfort and convenience for modern dwellings and are a standard specification for higher end properties. But this isn’t a new approach to heating rooms; indeed the earliest evidence of underfloor heating can be traced back some 7,000 years when trenches cut into floors covered with stone carried warmth from strategically placed fires.
Clearly a great deal has changed since those early days and there have been a number of major developments in the last 100 years that have resulted in the modern systems we know and enjoy today. But more recently, the most significant development in underfloor heating has to be the introduction of flowing liquid gypsum screeds. Superior in many ways to the more traditional sand and cement-based screeds, liquid gypsum screeds offer many benefits including cost, convenience and sustainability.
But arguably, the biggest advantage of a flowing liquid gypsum screed is that it can be force dried quickly and safely, provided the right equipment is used and best practice is observed. Force drying is suitable for these screeds as they do not curl and they need no reinforcement. In addition, shrinkage is extremely low and large bays can be laid without risk of cracking.
Screed drying times holding up projects are a big issue for contractors. Site running costs and penalty clauses for projects running over time can run into many hundreds of thousands of pounds and the associated uncertainty is a major problem for project managers trying to plan work schedules.
The drying times given on screed datasheets are generally based on a fixed environment, at 20ºC and 60% relative humidity throughout the stated drying period. But It is rarely, if ever, possible to achieve these conditions naturally on a construction site in the U.K. Typically an anhydrite (what gypsum becomes when heated) screed, installed at 50mm depth, will be said to have a drying time of 60 days, given these fixed environment conditions, but on a construction site this will often extend to 90 days or more.
The force drying technique can bring the total drying and commissioning time down to just 28 days. The key to successful force drying is using the correct specialist drying equipment, total control of the environment (including temperature and humidity) and appropriate moisture testing. These factors ensure that the necessary heating and cooling programme can be carried out with absolute accuracy in terms of results and timing. Furthermore, using this force drying process reduces the risk of floor failure and the associated expensive remedial costs.
Time is money in construction, so being able to shave up to around two months off installation and commissioning time for liquid screed floors by force drying represents a very significant cost saving for contractors and developers alike, and brings welcome certainty to any construction programme.
While force drying is often employed as an afterthought once it becomes clear that the reality of building in a UK climate does not match the screed manufacturer’s guidelines, the smart specifier will include force drying as an integral part of the project plan, allowing build schedules to be forecast with far more accuracy.
The developers of Barts Square in the City of London specified force drying across all 91 apartments to aid what was an extremely tight build programme, and guarantee certainty in regard to timing and quality control of floor installation and commissioning.
In the case of London’s two tower Hoxton Press development, the build programme was at risk of over-running, due to the 60 day drying times stated in the screed manufacturer’s guidelines not being met. Force drying was implemented across all 198 dwellings in both towers; typical drying cycles of 21 days were achieved, and the build project was able to proceed on schedule.
Underfloor heating is generally perceived to be a luxury specification, only appropriate for high-end properties. As a result, specifiers will often opt for radiators instead for lower cost dwellings, such as the affordable housing element of a project. However, underfloor heating systems with liquid gypsum screeds are quick and economical to install and can be an economically viable solution for all types of property – including affordable housing – given the right approach.
A recent study, comparing the costs of a radiator-based heating system with an underfloor heating system with liquid screed, showed that the differences in installation costs were negligible. However, when combined with force drying and taking into account the cost benefit of the resulting time saving, the overall cost of installing and commissioning underfloor heating was reduced dramatically.
This study proves there is no reason why specifiers should not opt for underfloor heating for any kind of housing. Liquid gypsum screed flooring combined with force drying makes underfloor heating systems economical to install. In addition, liquid gypsum screeds have excellent conductive properties making underfloor heating systems more efficient and economical to run. This clearly enables developers to offer a superior product specification.
Another advantage of flowing liquid gypsum screeds is that they can be laid more thinly than sand and cement – typically 50mm for the liquid screed as opposed to 75mm for sand and cement. On a multi-floor project, this can add up to a significant height saving which is clearly a benefit to architects looking to deliver as much space, and therefore value, from the project. Thinner flooring of course also means savings on overall floor weights.
Sustainability is a major consideration for developers and a further advantage of liquid screeds is that they are significantly more environmentally friendly than sand and cement. Liquid gypsum screed comprises 98% recycled waste material, requires less energy to produce and, because it is thinner, it uses less material. As a result, a 50mm gypsum screed contains 20Kg less embedded carbon per m2 than a 75mm sand and cement equivalent.
The latest force drying technology combined with flowing gypsum screeds is clearly the modern way to prepare a building for floor coverings.
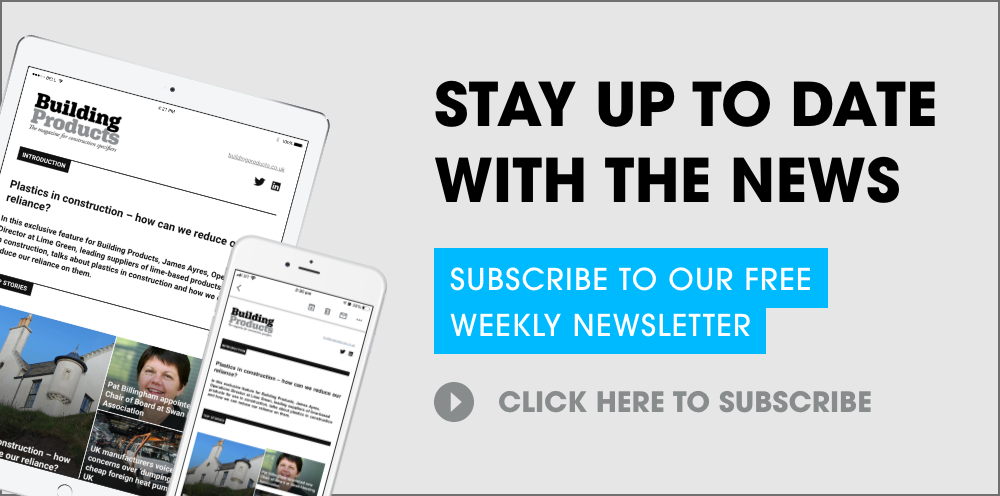