Countering Coronavirus and the race to install heat pumps and hydrogen heating

Written by John Osborne
Managing and eliminating coronavirus is as big a crisis as World War II was. John Osborne considers how recent developments in heating, ventilating, and air conditioning (HVAC) are helping control this deadly virus, and how heat pumps and hydrogen could change the way we heat our homes.
We cannot escape it. It is with us day and night. The pandemic dominates our lives. Sadly, it looks as if it will kill more civilians in the United Kingdom than were killed in the UK in World War II.
However, there is light at the end of the tunnel. The United Kingdom is full of brilliant people. The expertise is available to eliminate this enormous threat to our way of life.
B.E.S.A. is ahead in the battle. The Building Engineering Services Association claims it is the UK’s leading trade organisation for building engineering services contractors. B.E.S.A. represents the interests of firms active in the design, installation, commissioning, maintenance, control and management of engineering systems and services in buildings.
The main way the virus spreads is through air. “We have long campaigned on the subject of air pollution and indoor air quality,” explained Graeme Fox, Head of Technical, B.E.S.A. “We are about to publish A Beginner’s Guide to Indoor Air Quality produced in conjunction with the British Lung Foundation, Clean Air Day 2021, and Mitsubishi, to clarify the terminology used and the urgent need to address this public health emergency.”
Education and measures which are easy to understand and implement such as wearing a mask and social distancing are low tech solutions. There is more though to running HVAC systems than preventing the transmission of viruses.
Some technologies are emerging which will make it easier and more efficient for owners and occupiers of buildings to operate HVAC equipment. There are also numerous challenges.
Blake Standen, Solutions Engineer at BrainBox AI, said: “Even as IoT (Internet of Things) technology advances, commercial building HVAC systems are still, for the most part, fixed systems and programmed for a static environment, even though weather, seasons, and tenant behaviours are fluid and dynamic.
“The built environment has not kept up with technology advancements. The commercial real estate design model is still very segmented and focused on unique structures that are difficult to utilize efficiently.”
Blake added: “In addition, energy efficient technology opportunities during the design phase are often value-engineered out prior to the construction of the building due to budget constraints. All of these elements have led to the inefficiency of building HVAC systems that continue to contribute to higher energy bills and maintenance costs while negatively impacting the environment. HVAC systems account for 51% of the total energy usage in commercial buildings and 20% of global greenhouse gas emissions that originate from buildings.”
Chris Irwin, Vice President Sales EMEA & VP Global Marketing, J2 Innovations, believes that there “Is no one single trend that stands out but several that will have profound effects. The trend for increasing ‘modularisation’ of HVAC products with standardized factory fitted controls will continue, as all players (manufacturers, contractors, etc) seek to reduce on-site costs and simplify delivery of working systems.
“Another accelerating trend is the desire for easy remote access to sites for performance monitoring, alarms and fault diagnostics. Both factors require more sophisticated but easy to configure controls software with secure remote connectivity.”
He continued: “A newer trend, accelerating since the widespread adoption of IP (Internet Protocol) connectivity, and the increasing availability of more powerful ‘edge’ electronics hardware, is the disaggregation of the software and hardware required for HVAC control. Previously, each manufacturer would develop its own proprietary solutions but this ‘re-inventing the wheel’ approach is becoming prohibitively expensive. Specialist software suppliers will increasingly provide the basis for the controls systems, customised for each manufacturer’s needs and running embedded on ‘standard’ hardware platforms.”
Dennis Marcell Victor, Senior Research Analyst in Frost & Sullivan’s Energy & Environment practice, believes that the “Digital transformation of HVAC equipment and services will form the backbone in achieving various energy-related targets for the future. Original Equipment Manufacturers have started investing in technology that can increase the efficiency of products and explore new revenue streams.”
Dennis said that according to Michael Ellis, Executive Vice President and Chief Customer and Chief Digital Officer at Johnson Controls: “Digital offerings that integrate a number of systems are more of a priority than ever for organizations evaluating their investment plans for 2021”.
Another issue is the way HVAC is run.
“HVAC as a service (HVACaaS) is a subscription-based model for HVAC equipment that could be a game-changer for daring and innovative manufacturers”, explained Dennis. “Offering products and services as a bundle reduces the burden on the customer to operate, monitor, and maintain the equipment, as the manufacturer oversees all of it.
“With the demand for remotely monitored HVAC systems on the rise, the HVACaaS market could attract large buildings that plan to upgrade their existing HVAC systems. By 2026, an estimated 7–8% of the HVAC market revenues could be attributed to subscription-based services.”
Metering is another big issue concerning the HVAC business. Anthony Coates-Smith, Managing Director, Insite Energy, explained that: “On Friday, 6th November 2020, BEIS (The Department for Business, Energy and Industrial Strategy) released its latest amendments to the Heat Network (Metering & Billing) Regulations, which came into force on Friday, 27th November 2020. They require all “heat suppliers” (landlords including developers, housing associations, local authorities and managing agents) to install metering devices on existing non-compliant housing stock where it is cost-effective and technically feasible to do so, as well as to bill individual consumers based on their actual energy consumption. “
He added: “The timescales are short considering the work some building managers will need to undertake. We’re urging affected organisations to speed up the process of assessing their buildings to meet the deadlines. The amendments call for the installation of heat metering devices, which can be heat meters or heat cost allocators (HCAs) with hot water meters, by September 2022 in all existing (and mid-construction) buildings connected to a district heat network or communal heating system.”
Another concern is the increasing digitalisation of heat network metering.
Eleanor Blacklock, Project Manager at Insite Energy, says: ”Heat networks are growing, so an increasing number of new buildings will require the specification of metering and billing platforms. Over the past few years there has been a move from credit billing customers for their energy to installing smart prepayment or pay-as-you-go (PAYG) meters, which have traditionally required hard-wired wall-mounted devices to be fitted in each property.
“To make PAYG more affordable, flexible, functional, easy to install and cheaper to run than the established alternatives, there is a trend towards web-app based metering platforms, accessible via a smart device. Insite Energy and SAV Systems have recently developed the world’s first digital smart metering, pay-as-you-go web-app for heat networks, called KURVE, and the UK’s first installation at Greenside Views, a development in London, has just taken place.“
Advances in HVAC equipment should make our homes and offices, and other buildings, more comfortable and more efficient to heat and ventilate. In 2021, the battle to eliminate coronavirus and efforts to reduce our dependence on fossil fuels will continue on many fronts. Arguably the biggest challenge though will be persuading people to adopt measures designed to protect them, and implementing new and unfamiliar heating technologies. <
Meeting the skills shortage will be a massive challenge
Heat pumps were highlighted by Boris Johnson, the current Prime Minister in the United Kingdom, as a key technology for delivering many of the government’s decarbonisation goals. He wants the industry to be installing 600,000 a year by 2028. The Committee on Climate Change (CCC) has already set a target of one million a year by the 2030s towards an eventual total of 19 million to achieve the government’s net-zero targets.
This represents a “massive surge in the market that will both excite and alarm the industry”, according to Graeme Fox, Head of Technical, B.E.S.A. “We will have to rapidly scale up our capacity and we will need considerable investment in skills to deliver all of this,” he said.
Graham Wright, Former Chair of the Heat Pump Association, said “The sector was currently installing just 30,000 heat pumps a year, a figure that could grow to 71,000 in 2021”. He said “the CCC target represented an enormous leap when we are already contending with a skills gap.
“The H.P.A. was working with B.E.S.A. to set up a training scheme that could help upskill existing heating and plumbing engineers to carry out this work. He called on the government to make it mandatory to ensure installations were of sufficient quality so that the technology could operate to its full potential.
“If there are lots of poor installations, it could harm the reputation of the whole technology,” said Graeme.
Industry estimates suggest more than 17,000 new heat pump installers will be needed to meet demand over the next decade.
The Future of Heating
Martyn Bridges is Director of Technical Communication and Product Management at Worcester Bosch. He discusses the latest field trials of hydrogen and what potential this has for future heating.
A number of successful trials and tests have taken place. One such project was HyStreet in Northumberland, part of H21. H21, amongst other things, sets out to prove that the UK’s natural gas grid can safely carry 100% hydrogen gas. Hydrogen is a promising carbon-free alternative to the fuel we use currently, particularly because when burned its only bi-product is water.
HyStreet consists of three specially built houses which have seen over 200 tests to prove the safety of converting homes and gas networks to hydrogen. A number of prototype appliances, including our own, are installed and running there as part of the trial.
The potential for hydrogen in existing properties is promising. It is very difficult, by contrast, to lower the carbon emissions of an existing heating and hot water system with the alternative, an electric heat pump.
A large proportion of UK homes are powered by a gas fired
combi boiler, so anything other than replacing the system with a carbon free gas system is prohibitively expensive.
Trials such as HyStreet are accelerating the adoption of hydrogen. There may be no choice but to opt for a heat pump installation initially, and that brings with it a number of challenges.
The largest issue for housing associations would be the sheer cost of heat pump installations replacing boilers. There have been a handful of cases where a heat pump system was installed instead of a boiler, such as Leeds City Council. It undertook a small trial. Here, the cost per house was around £27,000, which is quite a large figure!
By comparison, early indicators show that replacing your existing boiler with a hydrogen-fired alternative will be more or less the same cost as replacing a boiler today would cost.
Another challenge for converting existing homes to an electric heat pump is disruption to the home owner and space limitations. Combi boilers are popular for their efficiencies. They provide both heating and hot water from one space-effective product. However, a heat pump requires a sizeable hot water cylinder, which would need to be located in a home either on a landing, airing cupboard or bedroom. It takes up valuable space which may not be readily available in the current home layout.
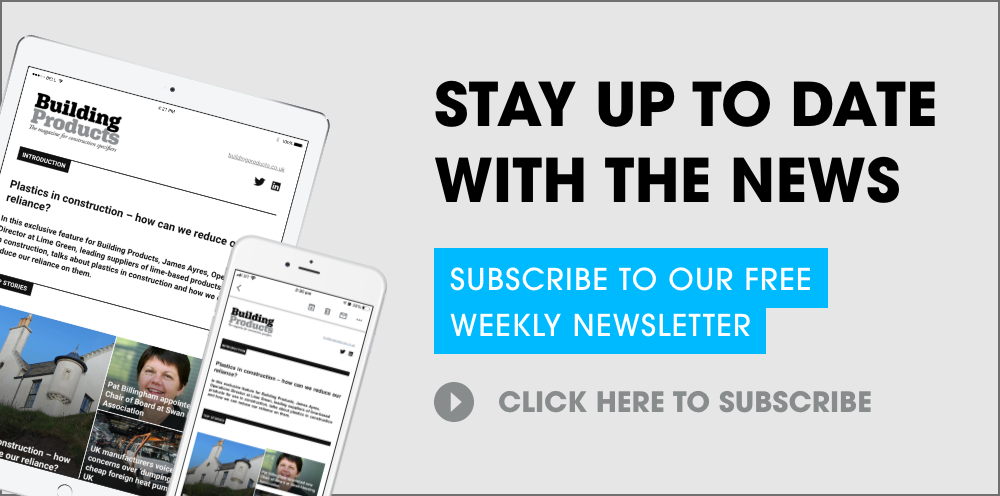