Dispelling the concrete SIP myths
Despite the popularity and growing use of concrete structural insulated panels (SIPs) in a wide variety of building environments, many developers, contractors, and builders continue to overlook them. Chris Williams, MD of Green Life Buildings (GLB), believes that common misconceptions are the reason they are ignored. Here, he explains why GLB’s very own revolutionary SIP panel building system busts the myths.
As an industry, construction has largely stayed on the side of the traditional. And it’s easy to see why; after all, traditional building methods and materials have worked for decades.
What that does, however, is provide a very rigid way of thinking and this is certainly the case when it comes to using concrete SIPs, and the certain perceptions of building with them.
As Managing Director of Green Life Buildings, manufacturers and suppliers of a revolutionary concrete EPS panel, Chris Williams has come across those misconceptions more than most.
“Concrete SIPs have been used to build millions of structures around the world, from domestic, industrial, and commercial construction, but there is still a reluctance to use them as opposed to bricks and mortar, for example,” said Chris. “That’s down mainly to a lack of knowledge of SIPs, and perceptions of them as a building product that are simply not true when looked at properly.”
GLB’s advanced building system uses prefabricated insulated panels enclosed in galvanised steel mesh with connectors which, once in position on site, are sprayed with a structural fine concrete coat to provide unbeatable strength.
The panels can form walls, floors, landings, roofs, stairs, and internal partitions can be curved to meet demanding architectural specifications, meaning a single family home can be constructed almost entirely from the material in just five-six weeks. The system can be made to any specification and tailored to work with any design, while its flexibility means it can be built on any site, no matter how difficult.
“Providing a building system that is cost-effective, better for the environment, and easy to install are the reasons behind our system,” said Chris: “And it proves that the misconceptions around concrete SIPs are exactly that.”
Size matters
When people think of concrete SIP panels, they think they are not suitable for small projects but this, says Chris, is wrong, particularly when it comes to the GLB panel.
“Our panels can be made to any size; we’ve got a dwarf basement storeroom going into Ireland and it’s only 1.8m high, so it’s not very many panels at all.
“With the GLB panel we can provide for small jobs or large jobs, there is no size requirement and, just as importantly, no price point. This means it’s not volume that drives the price.”
Crane pain
Concrete SIPs are thought of as too heavy to use without a crane, but the GLB panel takes that pain away thanks to its inherent lightness.
“A general panel weighs 3.4kgs per square metre before concrete coating, eliminating any need for cranes or other external equipment as everything can be carried on site by hand,” said Chris.
“Realistically, while we can make nine metre panels, they would be too cumbersome to lift on site so we can create the same effect with three three metre panels. We have installed six and a half metre panels 20 metres up in the air with a hand lift, so it is very doable. We couldn’t even get a crane onto the site, so there was no other way of doing it than using a Gin wheel off the side of the building.”
More money
Many assume that the cost of concrete SIPs is too expensive when compared with traditional building materials, but that’s not strictly true, says Chris.
“Concrete SIPs done as a precast panel are very expensive, and that’s largely because on the design regulations for them, they have to use 150-200mm of concrete.
“With our panel, however, we’re using just 80mm of concrete, so the cost of our panels is very low, and you’re not paying for somebody to make them, you’re getting a panel on site that your normal labourer, bricklayer, carpenter, plasterer can put up and finish off.”
A hefty footprint
There is also a view that concrete SIP panels have too high a carbon footprint, but this, much like the perception of concrete SIPs themselves, is wrong.
Chris explained: “People don’t truly understand carbon; concrete’s reputation proceeds it as the biggest polluter for carbon dioxide in construction materials, but that is only because of the volume of concrete used internationally. If you were to swap that concrete for another product, be that timber, brick, or steel, then their carbon footprints would result in a higher overall carbon dioxide equivalent emission than that of the concrete they replaced.
“Concrete has about 121g per kg of use, brick has 400-500, timber 400-800, and metals are greater than 2000 on average, so people need to understand what they mean by carbon footprint. It’s about how much you use as well as what you use.
“If I were to build a timber home then it would have a higher carbon footprint than if I built a GLB concrete EPS home because we are talking about actual emissions, not off-sets or sequestered carbon.”
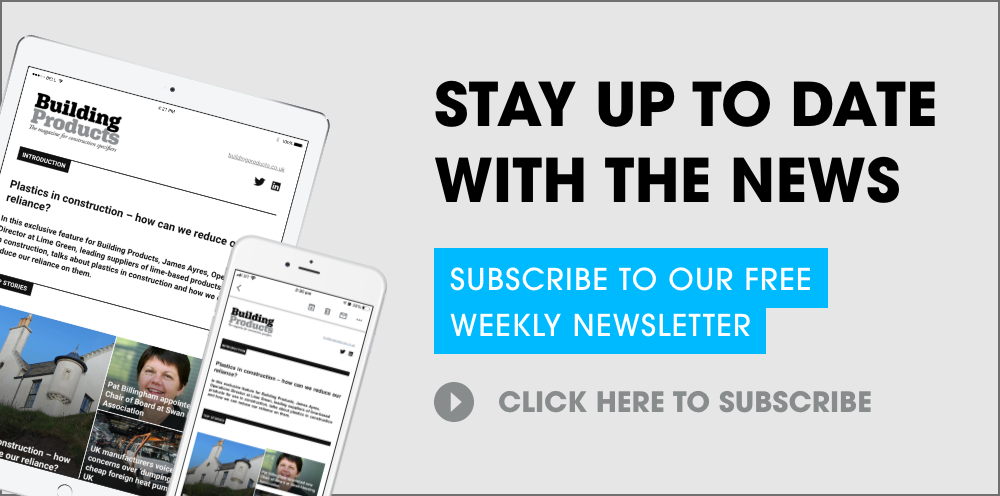