Making the future
As its name suggests, Factory 2050 could easily be considered ‘years ahead’, thanks to its futuristic architectural design and its advanced use as a state-of-the-art manufacturing facility.
Located in Sheffield, South Yorkshire, Factory 2050 is the first building to be constructed as part of the University of Sheffield’s new Advanced Manufacturing Campus and has become the new home of the University’s Advanced Manufacturing Research Centre (AMRC) with Boeing. The building is also breaking new ground by being the UK’s first fully reconfigurable assembly and component manufacturing facility, with its revolutionary flexible design enabling machines and manufacturing modules to be easily and rapidly adapted to suit the production needs of a wide range of industries, including aerospace and other high-value sectors.
As one of the most advanced facilities in the world, the AMRC Factory 2050 will combine technologies, including advanced robotics, flexible automation, unmanned workspace, off-line programming in virtual environments linked to plug-and-play robotics, 3D printing from flexible automated systems, man-machine interfaces, and new programming and training tools – all under one roof.
Designed by Bond Bryan Architects, the circular design of the building helps create a light and spacious interior, maximising the amount of usable floor space and ensuring the facility can be easily reconfigured. Moving away from traditional building design, the desire to create a truly flexible working space that is not limited by internal walls has been achieved by creating what Bond Bryan refer to as a ‘workspace doughnut’. The open-plan work space is positioned around a central core, where the lifts and staircases are situated along with the vital mechanical and electrical services to keep the floor space uncluttered and unrestricted.
Design detail
The exterior of Factory 2050 has been largely constructed from glass to create a striking focal point on the new campus and to showcase the innovative manufacturing work that is being undertaken within. The glass rotunda building will provide a base for reconfigurable, data-driven technologies, whereas the long, rectangular extension will accommodate any commercially sensitive or larger footprint projects. The two structures connect via a glazed link building.
Main contractor Interserve appointed building envelope specialist Lakesmere Group to design and install the facility’s complex facade package that features 8 m high glazing, spanning from ground to roof, and wrapping 360° around the entire building.
The architect’s vision to give the facade a strong horizontal emphasis has been achieved through the use of a 3 x 1 m glazing module. The main facade features a complex combination of Jansen Viss Ixtra, a steel curtain walling system spanning 8,000 mm, and Schuco FW50 and 60+ aluminium curtain walling systems. Lakesmere’s package also included the installation of the rooflights and balcony screen in the new conference area.
Having already worked on a number of high-profile and technically complex glass facade contracts, the specialist glazing team from Lakesmere North was tasked with delivering the fully glazed elevations of the main rotunda building and link building, working alongside sister-company McMullen Facades, which carried out the design function for and on behalf of Lakesmere.
On a project where accuracy and attention to detail was vital, Lakesmere’s close collaboration with both Bond Bryan Architects and main contractor Interserve helped deliver a robust design solution that identified any potential problems prior to work commencing on site. One risk that was flagged up early on was the fact that although the curtain wall components are precision CNC manufactured, the structural steel package is not, so both had to be perfectly coordinated. To ensure accuracy, the team initiated the coordination of all other disciplines tasked with delivering the various other packages that had interface connectivity with Lakesmere’s scope of works. This also included conducting an ‘as built’ survey position of the steel structure prior to manufacture with the view to capturing most of the tolerances and allowing this information to be transferred within the design for manufacture.
Rounded solution
Circular buildings always present unique challenges for facade design, and according to Gary Creaney, facade engineer with McMullen Facades, Factory 2050 proved to be no exception. “This was without question, a complex design owing to the circular design of the building and the fact that the glass and horizontal transom members are stepped incrementally in a facetted arrangement rather than curved to the natural radius of the building,” he said.
Owing to the design of the facade, the team identified early on that there was a potential risk that when the installation reached the last few vertical mullions, any slight imperfections in each bay would have accumulated over a large floor plan, leaving them out of position. To overcome this problem, and to ensure accuracy throughout the installation process, there was plenty to be done behind the scenes before work began on site. As only top and bottom connections were permitted, and indeed achievable, on the main rotunda and main entrance facades, the 8 m vertical span of mullions required structural analysis and design from which the Lakesmere team developed deep bespoke laser welded members.
“By designing adequate flexibility between the horizontal to vertical connections we allowed our installation team to position the mullions in the correct design location, eliminating any risk due to ‘creep’ or accumulative tolerances,” Creaney added.
Vision of the future
The futuristic structure of Factory 2050 has been further enhanced by its environmental credentials, having been designed to achieve a ‘Very Good’ BREEAM rating. With the glazed elevations ensuring an undisrupted flow of daylight, the facility also benefits from natural ventilation and heating, incorporating ground source heat pumps and wind turbines.
As striking as the building looks, the decision to wrap the circular building of Factory 2050 in glass was not merely for aesthetics. The facility’s fully glazed elevations provide the outside world with a fantastic view of the work that is going on within and this level of transparency is a deliberate attempt to attract and excite the next generation of skilled workers and pioneers, giving the manufacturing industry a much needed boost. As a landmark development on the global manufacturing stage, the new Factory 2050 scheme is most definitely ahead of its time.
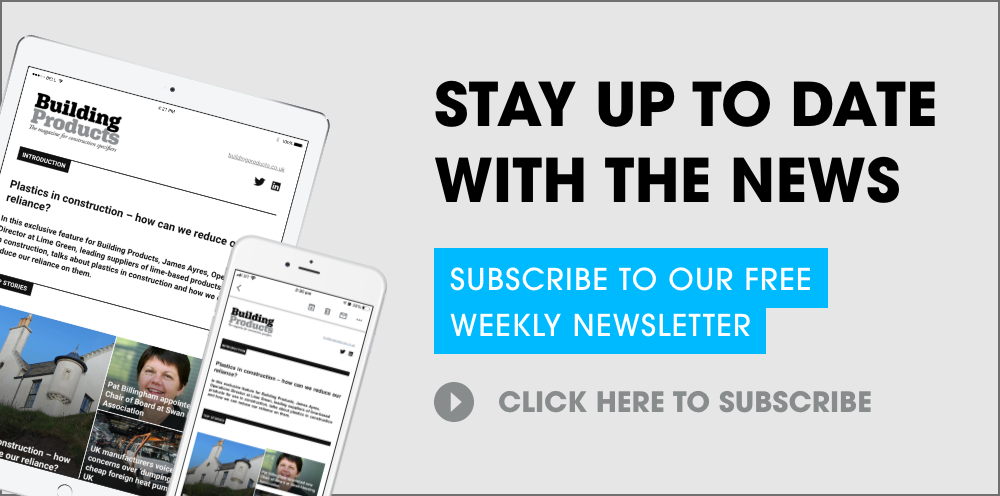