Reduce what you don’t need: How prefabricated pipework in modular assemblies can help the industry to become truly sustainable
With the construction industry facing greater calls to reduce its environmental footprint, there has been a noticeable increase in the drive to adopt more modern methods of construction. Dave Lancaster, Senior Segment Manager at Uponor, explains the green benefits of pre-fitting pipework and radiant heating systems into modular assemblies.
Modular construction has come a long way in recent years. Following the Budget 2021 and the government’s announcement of an MMC 1 taskforce together with £10m funding to boost the sector, off-site construction has never been in a stronger position to lead the way in sustainability.
Research carried out by AMA Research forecasts the MMC market to grow by 14% between 2020 and 2024. Much of this is expected to be driven by an increasing number of public sector procurement frameworks, more widespread adoption of BIM and the government’s commitment to making sure public works projects are delivered in a more collaborative, efficient and sustainable way, as set out in The Construction Playbook. In the future, we can expect to see more and more housing developments, schools, hospitals and care homes being built using this modern method of construction.
A change in perception
It is certainly the case that there is an existing perception of modular building out there that needs to be shifted, one which associates off-site construction with post-war era prefab. However, modular is not prefab. Of course, pre-fabrication is a form of modular process – it involves construction off-site – but the design and construction process involved with modular construction is vastly superior.
Modular construction is not just about building modules or pods off-site, it’s about constructing high-quality fully fitted-out structures. Manufacturers across the entire building spectrum are now realising the benefits of off-site manufacturing and construction, and as a result, we are seeing greater collaboration throughout the supply chain and the adoption of new technologies in order to provide high-quality, greener solutions.
Clearly, there are different approaches to installation on-site and modular assembly, which is in effect a factory and production line environment, but once people understand the benefits their attitudes towards piping prefabrication, and modular assemblies more widely, will shift. Pipework and radiant heating systems lend themselves perfectly to modern factory-based construction, for example, simple methods such as manifold plumbing reduce the number of fittings required, saving
on costs and minimising the risk of leakage.
When pipework is installed during off-site production, on-site waste can also be virtually eliminated and the minimal waste that might be produced can be easily controlled, which helps to avoid contamination and allows materials to be recycled appropriately and even re-used on future projects.
Installing off-site allows for greater precision and quality control as the off-site factory process often involves people specialising in one specific area to a very high standard. Pre-fitting pipework into modular assemblies in a controlled environment helps to minimise heat loss and maximise energy efficiency as the modules can be air tested for leaks before they leave the factory. By working closely with our partners during a modular assembly, we can also ensure that best working practices are upheld, therefore guaranteeing consistent product and installation quality.
Ensuring thermal comfort
When it comes to providing thermal comfort, underfloor heating (UFH) is the perfect solution for off-site construction methods, particularly as we look at more sustainable ways to heat a building. UFH produces radiant heating which heats (or cools) an area at a consistent temperature. The system can be controlled by room or zone, which could be a bathroom pod, kitchen or bedroom, through a thermostat that regulates each pod or room. This is a more efficient way to heat a building and reduces the amount of energy required. In fact, it’s estimated to be between 20-25% more energy efficient than convectional heating.
Optimum use of space
Various studies on climate change indicate that temperatures within indoor spaces will rise above the comfort threshold of 26°C and that the energy needed for cooling will, in the future, exceed the energy needed for heating. As a result of this, future-oriented temperature control must include both heating and cooling while being as energy-efficient as possible.
In new builds, a radiant cooling system can be installed under the floor or behind a wall or ceiling. This makes underfloor heating systems the perfect fit for modular constructions that are limited on space as not only do they take up less room than convectional heating systems, such as radiators, but it is relatively easy to use an underfloor heating system for cooling too.
Reaching new heights
We are already seeing the advances that have been made in modular construction and what can be achieved through a close supply chain partnership. Vision Modular Systems UK was recently involved in the construction of what is currently the world’s tallest modular building, Ten Degrees in Croydon.
The development features 546 apartments in two towers of 38 and 44 storeys, and by working closely with its suppliers, the company was able to design and deliver 1,500 completed modules to site in just 24 weeks. This included the off-site installation of bathroom pods and kitchens, wiring and plumbing comprising Uponor’s pipework and manifolds for hot and cold water systems.
By working in collaboration with its suppliers, Vision has now been able to develop a template for its modules, and roll out this approach across future schemes.
This form of volumetric construction is becoming more popular. Bathroom and kitchen pods, or bedroom and classroom modules, can be pre-fitted with plumbing, heating, electrics, doors and windows, and commissioned before leaving the factory to ensure there are no defects. Careful programming and scheduling can ensure efficient production and allow the units to be designed in a way to maximise the use of space on delivery vehicles, also helping to reduce carbon emissions.
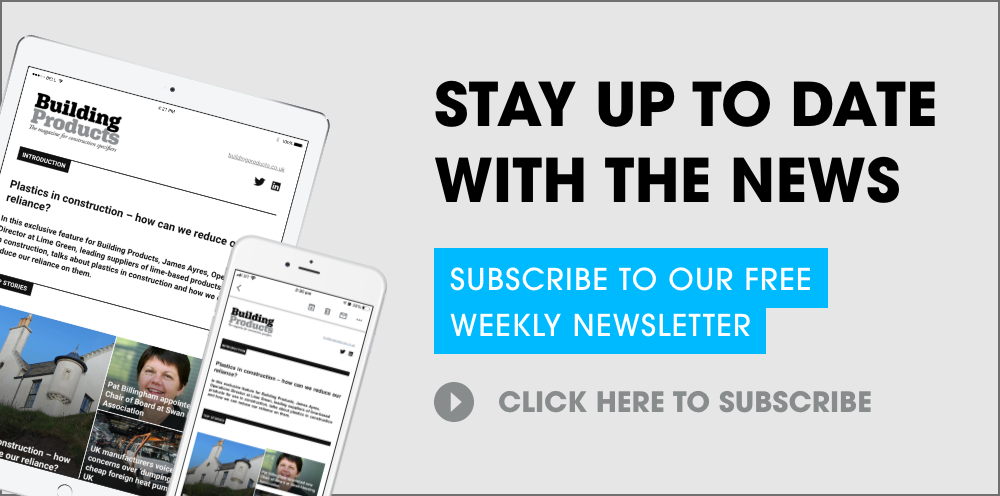